Across the passenger car marketplace, battery-powered electric vehicles (EVs) and hybrids are eating away at the market share of gasoline-powered vehicles. This redesign of a car’s powertrain makes a lot of sense — EVs reduce emissions and fuel costs. But when it comes to the heavy-duty engines powering ships, excavators or tractors, the path to a greener future isn’t quite so simple, says Dr. Adam Dempsey, assistant professor of mechanical engineering.
Dempsey’s familiarity with these hard-working engines started long before he set foot in an engineering lab. Growing up in rural Illinois, he spent a lot of time around farm and construction equipment run on diesel engines, which differ in significant ways from gasoline engines in passenger cars. “The reason diesel engines are used for agricultural equipment or marine applications is because they have really high torque and power at low engine speeds,” Dempsey explains. These diesel engine operating characteristics are needed to meet the heavy-duty vehicle’s requirements for performance. “And a tractor or a mining truck has to operate for an eight- or 12-hour shift without stopping.”
For these reasons, a battery-powered alternative won’t suffice, but Dempsey is working on a different sort of solution. Supported by $2.5 million in funding from a U.S. Department of Energy grant and a $2 million Office of Naval Research grant, Dempsey is developing fuel-agnostic diesel-style engines that can work on scales ranging from a tractor to a 1,000-foot naval ship, while running on a lower-emission mix of fuels such as gasoline, ethanol, methanol, propane and more. And these aren’t the only examples of his leadership in pursuit of cleaner, better-functioning combustion engines: He is also principal investigator on a $4.2 million project funded by the Department of Energy to create technology that significantly reduces methane emissions from lean-burn natural gas engines used in the pipeline industry.
“These partnerships [with John Deere, Caterpillar and others] help streamline the process of taking technologies from the lab to the market, where it can have an impact on society.”
Dr. Adam Dempsey
But before he can reduce methane and carbon emissions from diesel-style engines, Dempsey must first convert them to run on fuels such as ethanol, methanol, natural gas and propane, but while maintaining a combustion process like a diesel engine. In their work to reimagine engines for farm and construction equipment and naval vessels, Dempsey and his team are hardly designing these machines from the ground up. Instead, they have developed a device that helps bridge the gap between the functionality and performance of a diesel engine and the environmental benefits of lower carbon fuels, which tend not to be compatible with diesel engines.
Developing ignition assistance technologies
“These fuels are not typically interchangeable because in a diesel engine, the fuel is directly injected and it must ignite on its own, but in a gasoline engine, spark plugs ignite the fuel,” Dempsey says. The low carbon fuels of interest, such as alcohols, natural gas, propane and others, are very hard to auto-ignite and thus more suited to spark ignition engines. “We have to add what I call ignition assistance technologies to the engine to get it to operate on these hard-to-ignite, low carbon fuels so the engine runs like a diesel on the new fuels.”
Essentially, Dempsey explains, this ignition assistance technology is a device added to the chamber of each cylinder of a diesel engine that acts as a pre-combustion chamber, which contains a fuel injector and spark plug to jump-start the engine’s auto-ignition process when hard-to-ignite fuels are used.
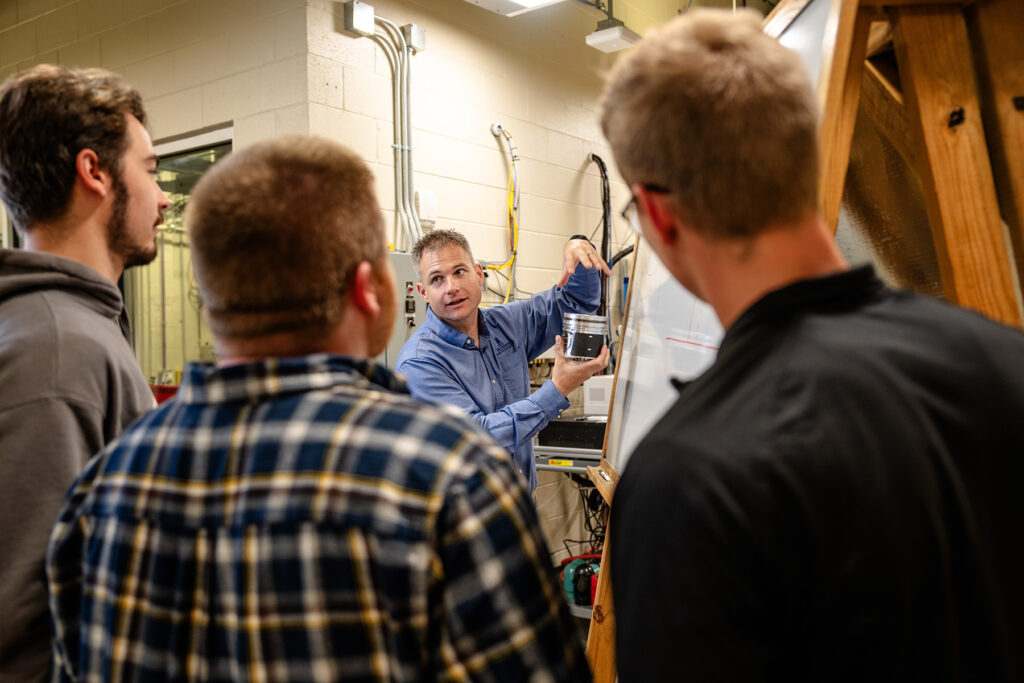
“We essentially put a little bit of fuel in the prechamber device at the right time and spark it,” Dempsey says. “It generates burning jet flames that penetrate into the main combustion chamber. At that point, it doesn’t matter what the fuel is — when you directly inject any fuel into that flame it’s going to ignite.” Therefore, this concept is fuel agnostic, and the engine can run on any fuel or fuel blend — while still performing like a diesel engine.
Dempsey developed this ignition assistance device through a project — funded by a $2.5 million Department of Energy grant in 2022 — that focused on reducing carbon emissions from diesel-style engines in farm equipment without sacrificing performance. The engine they are developing will run on any blend of gasoline and ethanol — up to and including pure ethanol. By operating the engine on pure ethanol, lifecycle greenhouse gas emissions will be reduced by 50% compared with diesel fuel. Partners include John Deere Power Systems, MAHLE Powertrain, the University of Wisconsin–Madison, ClearFlame Engines and the Missouri Corn Merchandising Council. Dempsey is looking forward to a future phase of this research that incorporates this technology in diesel-style engines for farm and construction uses that run on blends of propane and dimethyl ether. Both fuels are lower carbon alternatives to common fossil fuels; together they have the potential to lower greenhouse gas emissions from diesel-style engines by as much as 50% as well, but only after these alternative fuels become more widely available, Dempsey says.
The challenge to scale up — and achieve industry adoption
For these truck- and tractor-sized vehicles, the ignition assistance device can fit in the palm of your hand. But for the shipping vessels that are the subject of the Office of Naval Research grant, this device will need to be much, much bigger. “These ship engines are 100 feet long by 50 feet tall. They make tens of thousands of horsepower, and the pre-chamber might be as big as you and I,” Dempsey says. “So, the scale is just massively different, and we need to do the engineering work to design and scale this technology across a wide range of engine sizes.”
Dempsey and his team will need to study the physics behind these engines to determine how to scale their ignition device. Another problem to solve, he says, is how to make these engines truly fuel agnostic. “The Navy project is a new one for us because they would like it to be truly fuel agnostic with backwards compatibility to heavy fuels like diesel,” Dempsey says, meaning the engines would be able to run on any low carbon fuel and diesel. “It gives the Navy what they call ‘battlefield resiliency,’ which is a priority for the armed forces while they pursue their decarbonization goals.”
Creating this kind of backwards compatibility can be difficult, Dempsey says, because heavy fuels like diesel don’t evaporate as effectively as some of the low carbon fuels of interest, like methanol. When these heavy fuels wet the walls of the pre-chamber, it can become difficult to ignite the fuel and will form debilitating carbon deposits in the prechamber.
As for the smaller diesel engines, Dempsey says the obstacles involved in industry adoption of new technologies loom larger than the technical challenges. “That’s why partnerships involving equipment companies such as John Deere, Caterpillar and others are so important,” he says.
“These partnerships help develop technologies together and help streamline the process of taking technologies from the lab to the market, where it can have an impact on society.”